CNC Turning Service
- Instant online quote & DFM
- Parts in as fast as 2 days
- Tight tolerances
- Your IP is safe with us
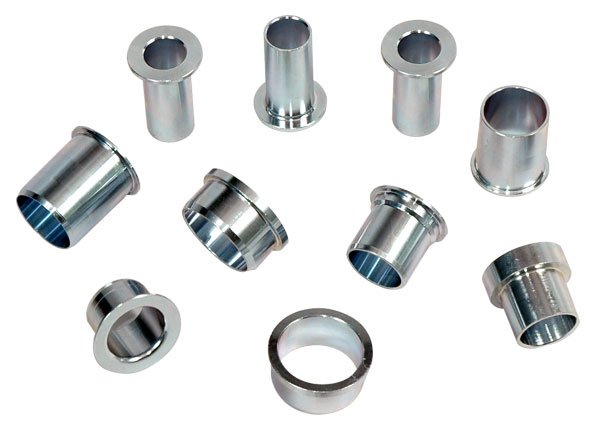
Certifications
ISO 9001: 2015
IATF 16949:2016
40,000+
Machined parts each month
50+
CNC machines
100+
Plastic and metal materials
What is CNC Turning?
The Basics of CNC Turning
A CNC lathe, commonly known as a CNC lathe machine, is a suitable tool for machining symmetrical cylindrical or spherical parts. In this type of lathe, the workpiece rotates on a horizontal or vertical axis while a stationary cutting tool moves in a linear or curvilinear path around it. The process of machining a workpiece on a CNC lathe is referred to as turning.
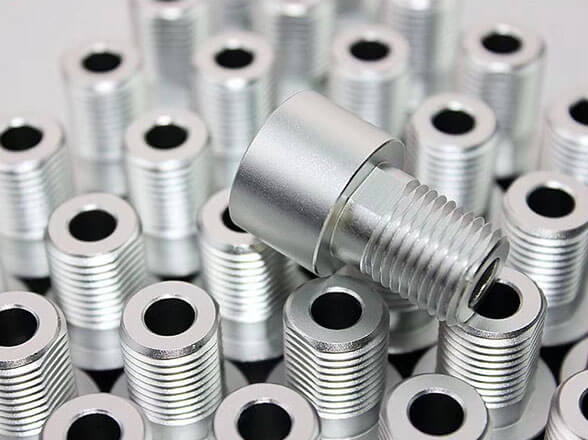
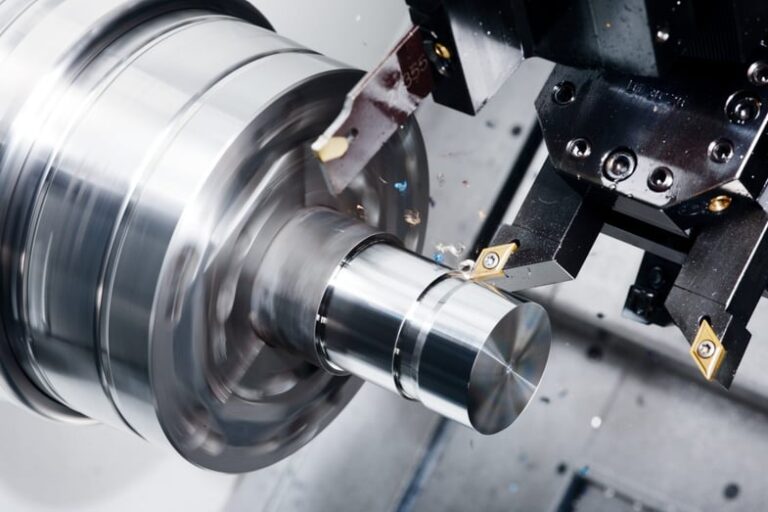
How CNC Turning Works
CNC lathes utilize a subtractive approach to shape the workpiece as desired. Firstly, a G-Code program is generated, and a raw bar of stock material is loaded onto the lathe's spindle chuck. The chuck holds the workpiece firmly in place while the spindle rotates. As the spindle gains speed, a stationary cutting tool is brought into contact with the workpiece to eliminate material until the intended shape is obtained. CNC lathes offer several operations, including facing, threading, knurling, drilling, boring, reaming, and taper turning. Different procedures necessitate tool modifications, which can raise costs and setup time. After all machining operations are complete, the finished part is detached from the stock material and subjected to further post-processing. The CNC lathe can then repeat the procedure with minimal or no setup time in between.CNC
All CNC Machining Services
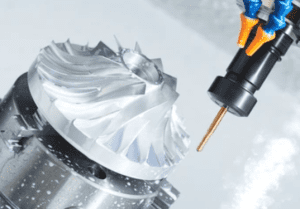
CNC Milling
3, 4 and 5-axis machining of plastic and metal parts. Machine up to 66" in size*
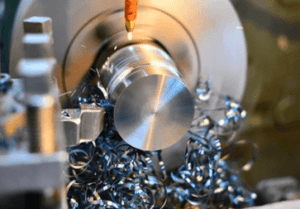
CNC Turning
Tight tolerances and finishing capabilities, as fast as 2 days.
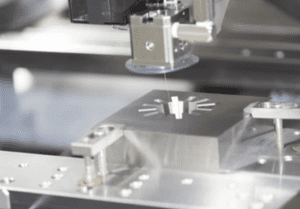
Wire Cutting
Add anodizing or powder coating to your item for a variety of finishes.
CNC Service Applications
Low Volume Production
RP Group offers full production-quality parts in volumes ranging from a single piece to a few thousand pieces.
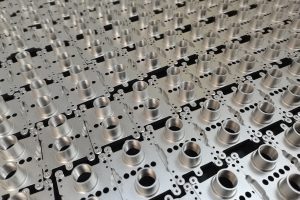
Appearance Prototypes
We take pride in producing the finest appearance models and prototypes with very high detail in any material you want.
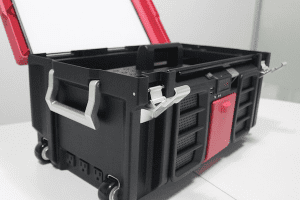
Fixtures and Gauges
We engineer fixtures and gauges to your specifications and may offer recommendations based on our in depth understanding of Geometric Dimension and Tolerancing (GD&T).
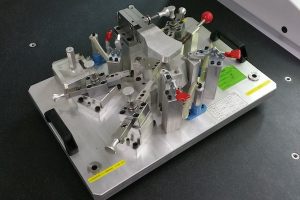
CNC Machining Materials
Metals
- Aluminum
- Brass
- Copper
- Stainless Steel
- Steel Alloy
- Magnesium
- Titanium
Plastics
- ABS
- Acetal
- CPVC
- HDPE
- LDPE
- Nylon
- PEEK
- PEI
- PET
- PMMA
- Polycarbonate
- Polypropylene
- PPSU
- PS
- PSU
- PTFE
- PVC
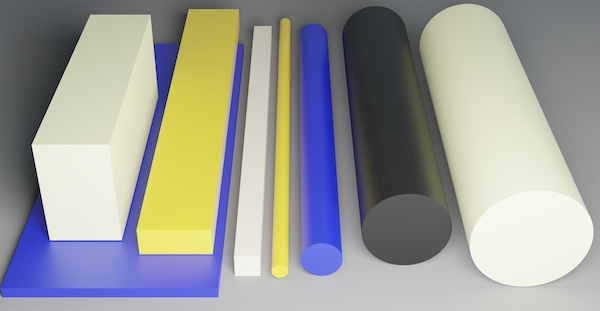
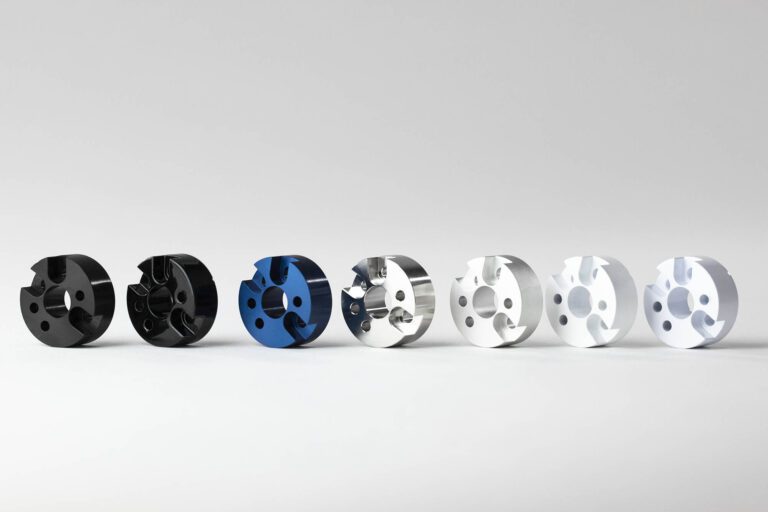
Finishing Options
At RP Group we can generate instant quotes for 10+ surface finishes. We can help you select the right finishes for your applications.
CNC Precision Machining Tolerances
At RP Group, we use ISO 2768 standards for CNC machining.
The length of parts that RP Group accepts depends on the machining process, with some processes accepting parts up to 48 inches in length. For larger parts, it is recommended to get in touch with RP Group's team.
It should be noted that the tolerances indicated are minimums in an optimal scenario and looser tolerances may be necessary based on the process, material selection, or part geometry.
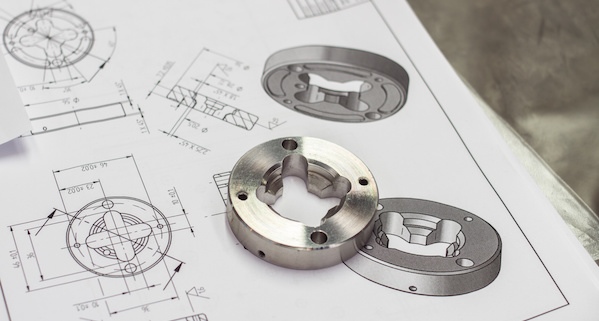
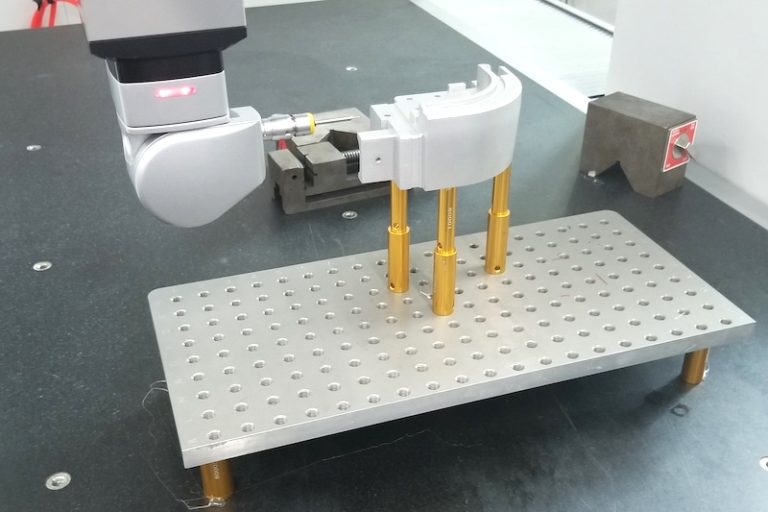
Metrology
At all four of our RP Group manufacturing locations, we have a fully equipped metrology department to ensure your part's quality compliance. Experienced engineers in fixture and gauge design from GD&T.
- Programmable
- 3D Scanning
- Fixture and gauge manufacture
Why choose RP Group for CNC Turning?

Design for Manufacture
Our experienced engineers will analyse your design and provide feedback on manufacturability and look for opportunities to reduce cost.

Communication
We are always quick to respond to questions via email, phone, web meeting or chat to ensure your project turn around is as fast as possible.

Quality Reports
All projects where 2D drawings are provided come with a dimension report before parts are shipped. CMM reports can be produced on demand at no additional charge.

Transparent Progress Reports
We provide progress and tracking information through our customer portal. Videos and photos of the parts can be confirmed before parts are shipped out.

Time to Market
We have a infinite capacity via our vetted supply chain outside our own in house capabilities so we have the flexibility to manage all projects large and small.

Full Service Manufacturing
We can offer a wide range of materials, processes, finishes and sub-components to make us your one-stop supplier for your whole project.
Design for Manufacture (DFM) is important part of product development to save money and improve quality
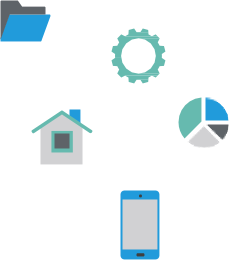
CNC Turning FAQs
Our usual suggestion is to use a minimum wall thickness of 0.5mm for metals and 1mm for plastics. Nevertheless, these values are mainly influenced by the part's size, hence as the part size increases, the recommended minimum wall thickness should also increase. It's worth noting that lower wall thickness values can still be feasible. These recommendations act as limits to mitigate the likelihood of warpage
CNC Turning Centers are utilized for performing turning operations. These machines, also known as CNC lathes, are equipped with a turret that holds tooling that is controlled by a computer. CNC Turning is a manufacturing process that involves rotating workpieces while utilizing various tools to eliminate material and shape the workpiece to the desired form.
During rough turning, the objective is to eliminate as much material as possible without emphasizing accuracy or surface finish, bringing the workpiece close to the intended shape. Finish turning, on the other hand, is the final stage of the process, which produces the desired smoothness and accuracy of the workpiece surface
Apart from using turning tools, a CNC turning center can also incorporate rotating cutters, such as drills or end mills, resulting in increased flexibility in machining. This feature permits the handling of asymmetrical characteristics in parts, thereby enhancing production efficiency, cost-effectiveness, and operational safety. Various aspects of turning differ from milling, including the ease of achieving radial symmetry, high precision due to mounting the part in the chuck, and the ability to obtain a superior surface finish.
CNC turning is a widely used process for producing an array of parts, such as auto components, knobs, tubes, gears, toy parts, flywheels, crankshafts, hubs, and disc cams. This process is primarily utilized in the manufacturing of parts for several industries, including automotive, aerospace, medical, and many others.